Composition and Advantages and Disadvantages of Stepper Motor Closed Loop System
Stepper motors are basically driven by open-loop circuits for position control . In other words, motors other than stepper motors, especially high-precision stepper motors, do not do open-loop control for positioning, and the only motors that are driven with open-loop circuits are stepper motors.
Brushless motors, for example, require the rotor position to be measured as well as a closed-loop position circuit containing a position sensor. Moreover, if it is driven at a certain speed, the speed of the rotor needs to be measured, and if positioning control is desired, closed-loop circuits with encoders and other sensors containing rotor position signals are required. Compared with open-loop driven stepping motors, closed-loop circuits containing sensors are more costly. Therefore, stepper motors are called low-cost drive systems for speed control or position control.
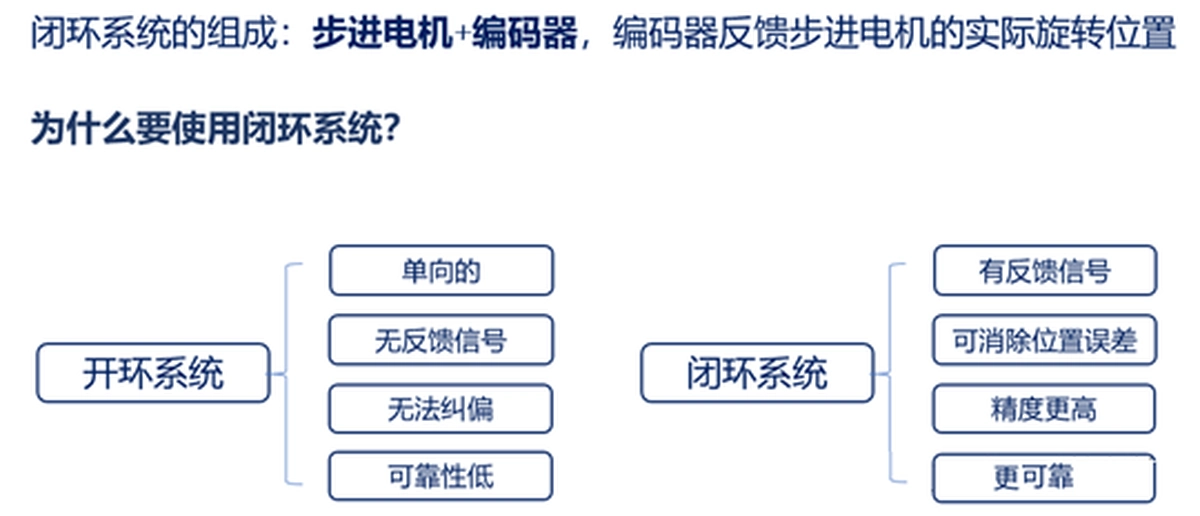
Advantages and disadvantages of open or closed loop systems
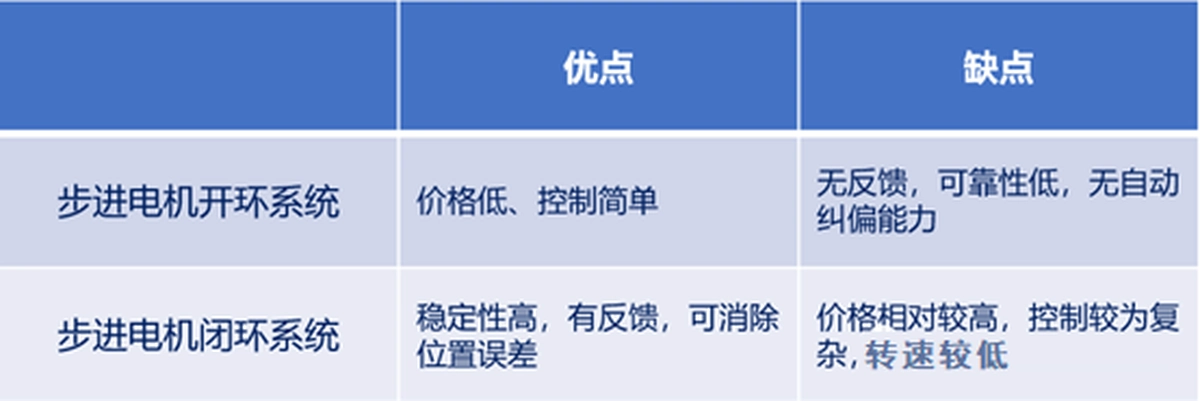
The open-loop circuit drive of a stepper motor has problems such as out-of-step, vibration (noise), and difficulty in running at high speeds when rotating at high speeds. To compensate for these disadvantages, angle sensors can be installed on the stepper motor to form a closed-loop control that is used to detect these problems to avoid out-of-step.
There are two general types of closed-loop control for stepper motors:
- Keep the phase relationship between the excitation flux and the current consistent, so that it produces an electromagnetic torque that can drive the load torque, this way of controlling the motor current is the same as the brushless DC motor control method, which is known as the brushless drive method or current closed-loop control method.
- The motor current is maintained at a certain level, and the method of controlling the phase angle between the excitation flux and the current is called the power angle closed-loop control method. The power angle is the phase angle made by the mutual attraction of the rotor magnetic poles and the stator excitation phase (or the stator rotating magnetic field axis of the synchronous motor can be considered).
Position loop control flow
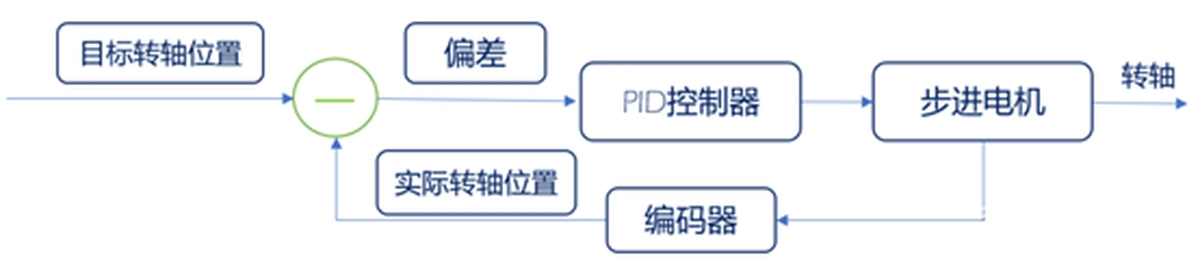
9 Advantages of Closed Loop Stepper Motor Drives
Servo motors rely on encoders to work, and closed-loop control stepper motors with encoders (stepper servo motors) have the advantages of both stepper motors and servo motors.
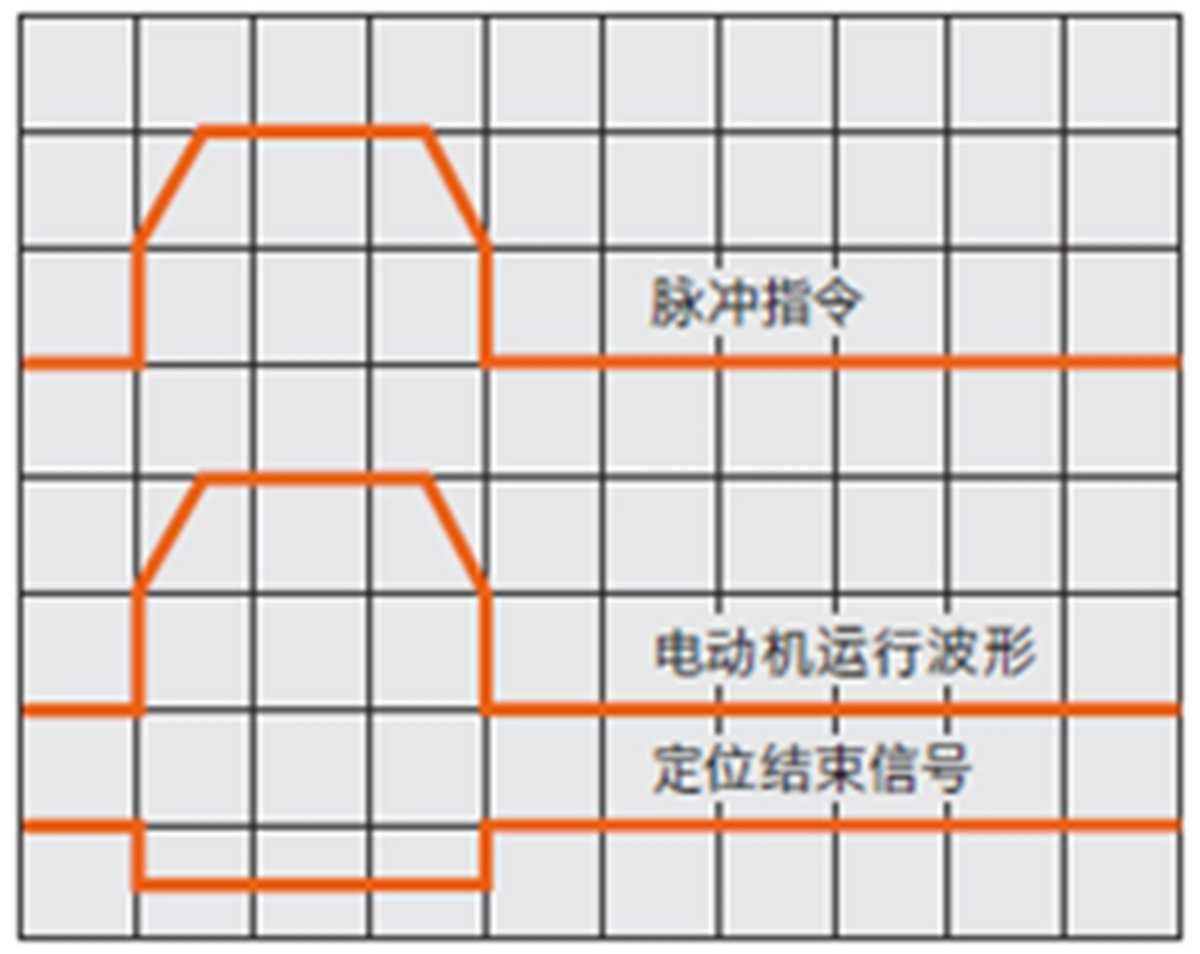
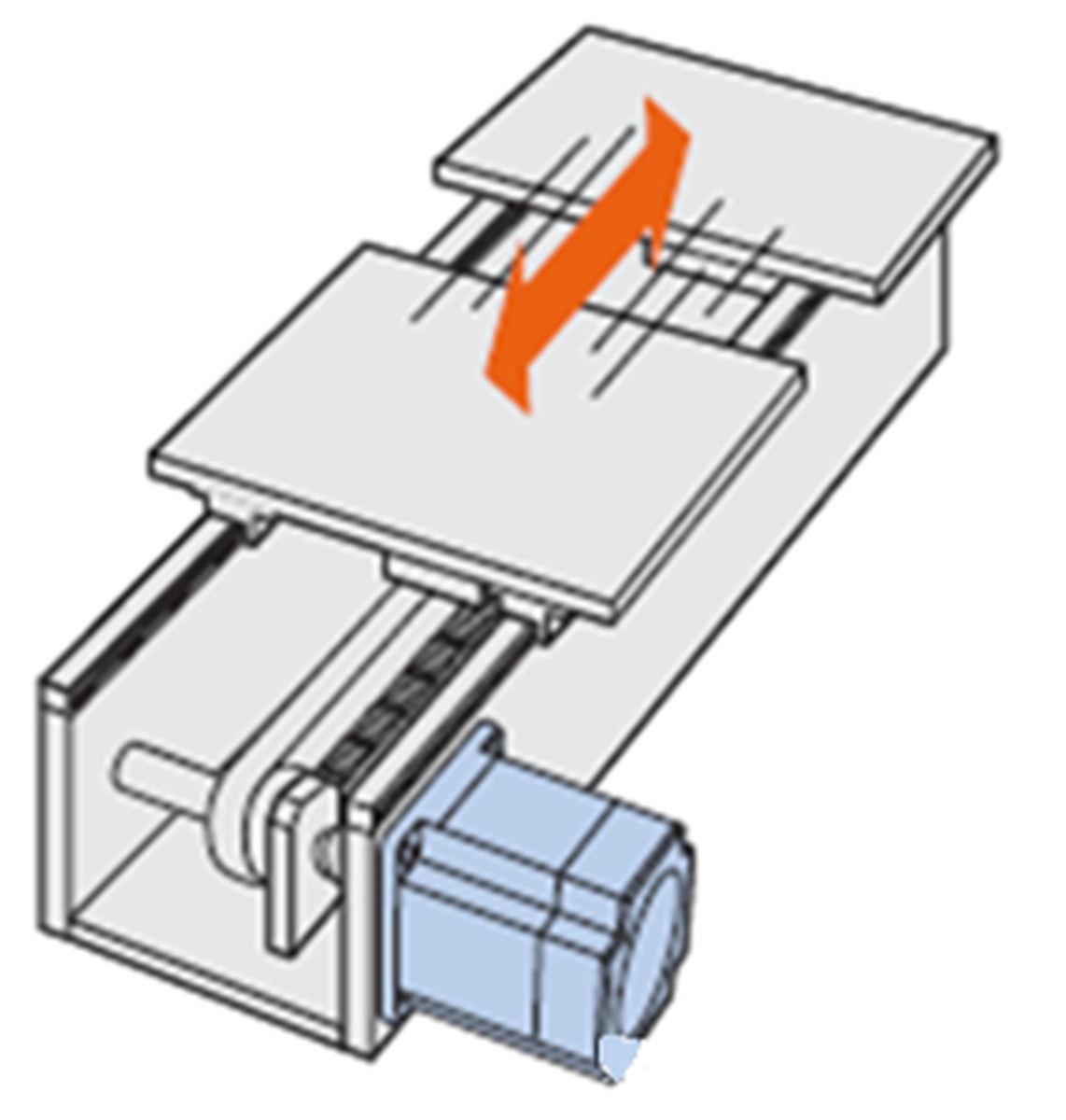
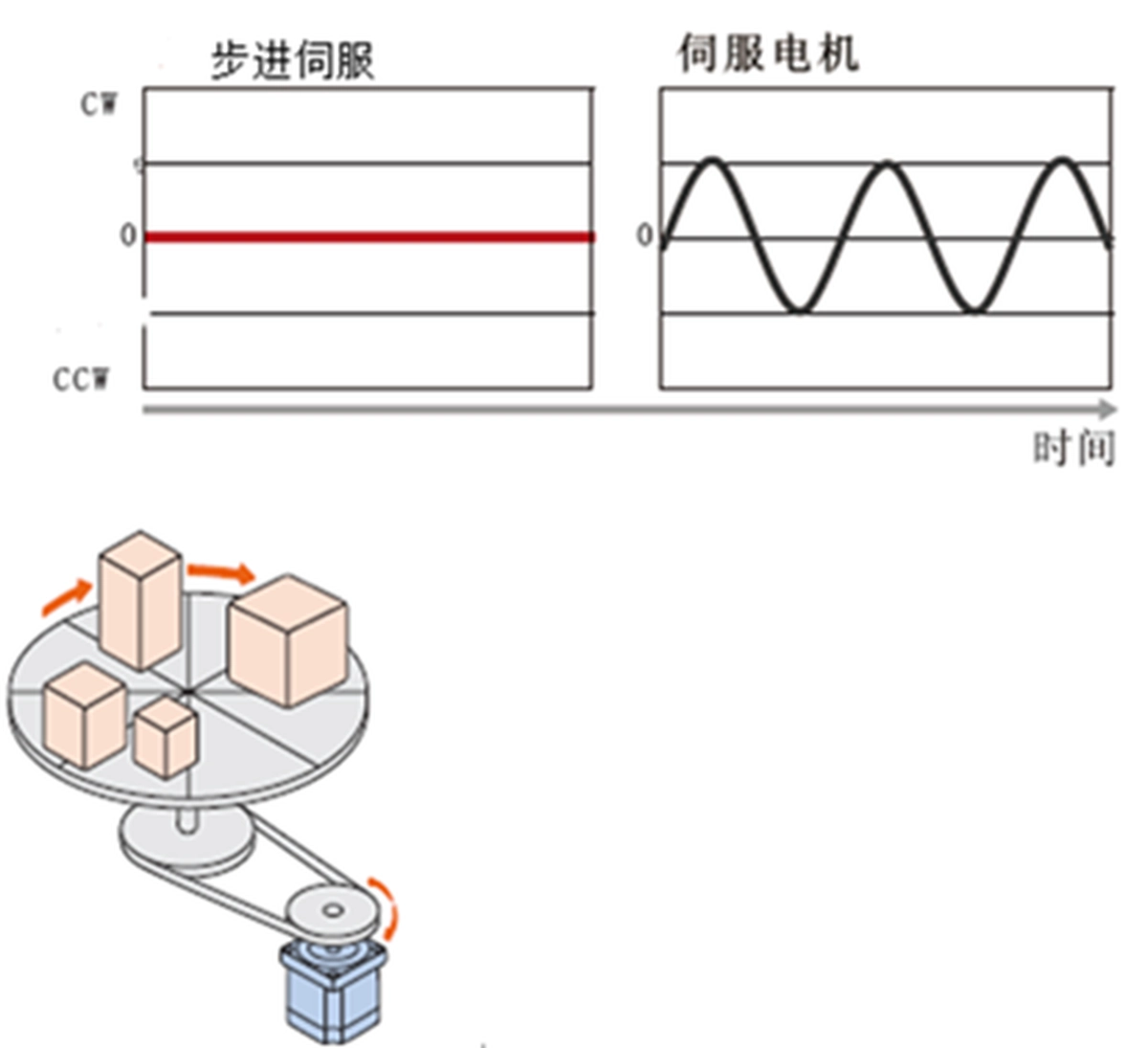
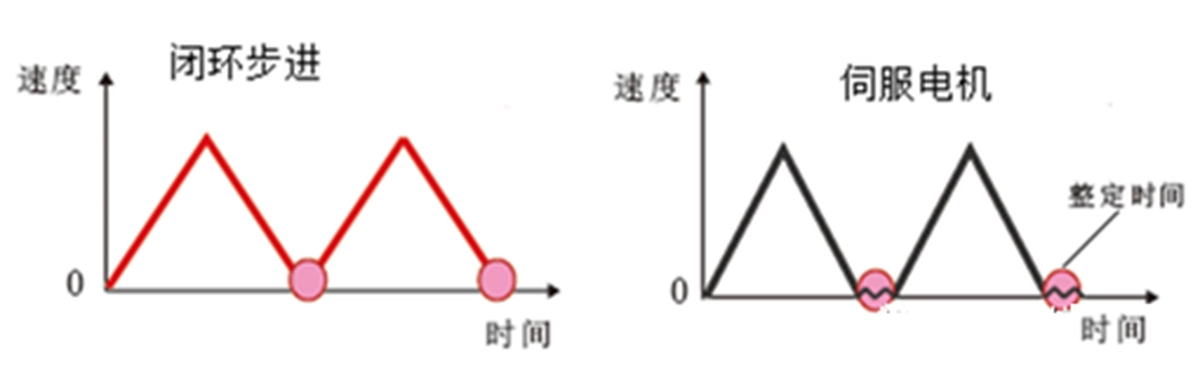
- Closed-loop stepper motor drives are suitable for applications that require frequent starting or stopping.
- Positioning can be achieved without gain adjustment even when the load changes in the belt mechanism, cam or chain drive. In servo motors, the gain of the servo system has a great influence on the performance of the motor, and adjusting the servo gain is a time-consuming and labour-intensive task.
- Servo motor in the stop due to rely on the encoder positioning needs gain adjustment, so can not be absolutely static, and stepper servo motor positioning without small vibration, through the motor itself to maintain the force stop, so the most suitable for the need to stop without vibration of low rigidity institutions, typical applications such as the optical field and so on.
- Compared with the same installation size of the servo motor, stepper servo can drive a larger inertia of the load.
- High speed .hanks to the continuous stable and reliable current control technology, the closed-loop stepper motor can run up to 3000-4000RPM without losing steps.
- As with open-loop stepper motor, closed-loop stepper motor and control instructions synchronous operation, so it can be in a short trip, short time to complete the precise positioning. Usually, servo motors are not suitable for short travel positioning due to the position fixing time when stopping.
- Compared with the traditional stepping motor, closed-loop stepping motor can output a large torque in a very wide speed range, drive can be 100% of the load continuous operation. There is no need to worry about the motor's ability to drive the load, which is completely different from the traditional micro-stepping (subdivision) drive. Stepping servo can be based on the motor speed using a unique current control technology to achieve high speed range can still output large torque.
- Because the driver uses vector control technology, can ensure that the motor at low speeds without vibration, quiet effect.
- Closed-loop stepping and Coolstep technology (current dynamically adjusted with the load) combined to reduce motor heating, reduce motor operating temperature, improve efficiency and further energy saving.
Recommended closed-loop stepper motor drive solutions
The traditional closed-loop method is the controller, driver and motor split, the controller sends out pulses/direction control driver, the stepping motor will encoder signal feedback to the driver, there are cumbersome wiring, after-sales service is inconvenient, the pulse signal is easy to strong magnetic field interference leads to positioning inaccuracy and many other shortcomings, and at the same time, because the encoder signal is fed back to the driver belongs to the semi-closed-loop, can not detect the loss of pulse in the control part.
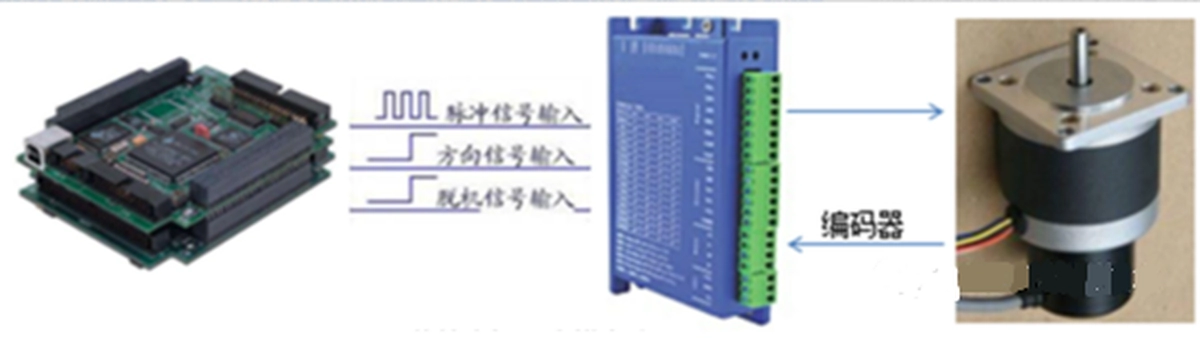
Traditional semi-closed-loop stepping solution
Adopting position full closed-loop control mode, the module integrates bus interface, motion control function, input/output, motor drive and programme storage, and the encoder signal is fed back to the module to complete the closed-loop control, which has the advantages of simple wiring, precise control, convenient after-sales maintenance and so on.
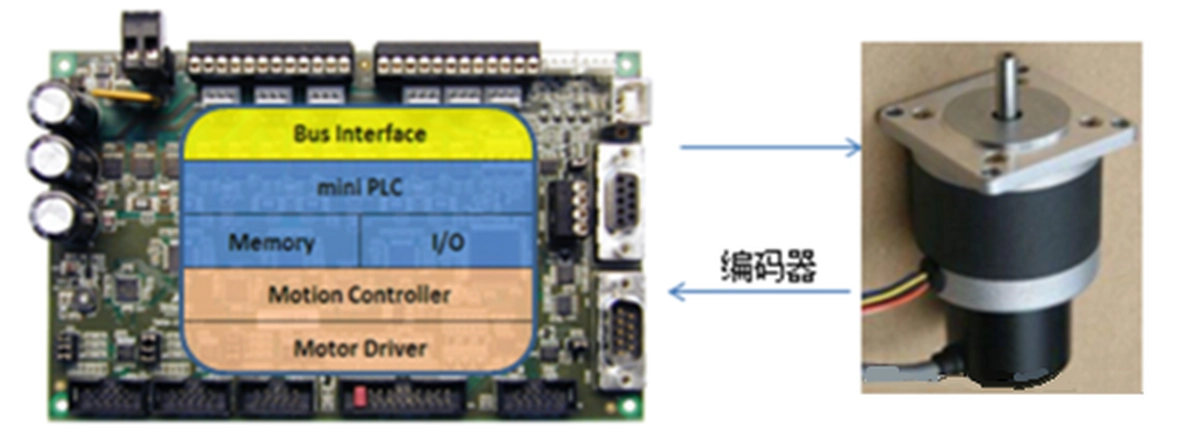
Leave a Reply